CORE-BOND / Reflow Core
TOURING ARTISTS FEEDBACK
"I have a tuner on my guitar, I randomly would return to alternate tuning and back. The strings were tuned to 12 different tunings several times. Always settled in tune and held regardless of the shifting around. I've had over 2 months of play on them and don't want to take them off until they break. They sound fantastic" - Michael Carr
"Until now, I thought the strings I used were the best strings ever made but quite honestly Core-Bond strings are even better. They still felt like new and had no discernible loss of tone. I seriously rank them at 10+ and when they become available they will be my string of choice for sure! Whoever designed these strings is a GOD!"- Mark Knapp
"The strings are great, especially the strong tone through the guitar pickups. The strings have been on my guitar for 5 Months and they still hold their tone with no corrosion or loss of tone." - Terry Lauderdale
WHAT CAUSES A STRING TO LOSE ITS TONE
Tone loss is when the wrap and core coupling is compromised either through mechanical degradation from the vibration of the string or galvanic corrosion due to the dissimilar metals used in the manufacturing.
Core-Bond ™️ addresses this issue by effectively "locking" the relationship of the core and wrap wire as "one". The buildup of dirt, skin cells, and acidic content in your hands get down between the windings and effectively dampens string tone as well as starts the corrosion process of the core wire.
The string isn't mechanically dead, however, the tone is compromised until the strings are cleaned which can be a difficult process to complete.

With the wrap wire removed, the magnification image above shows our high carbon steel core and the valleys Core-Bond ™️ create. Our secondary flow process liquifies and reflows Core-Bond ™️ into the grooves and locks in the wrap wire. The core wire is now surrounded and protected by Core-Bond ™️ against galvanic corrosion and premature tone loss caused by outer wrap slippage.
LEADING BRANDS OUTER COATING
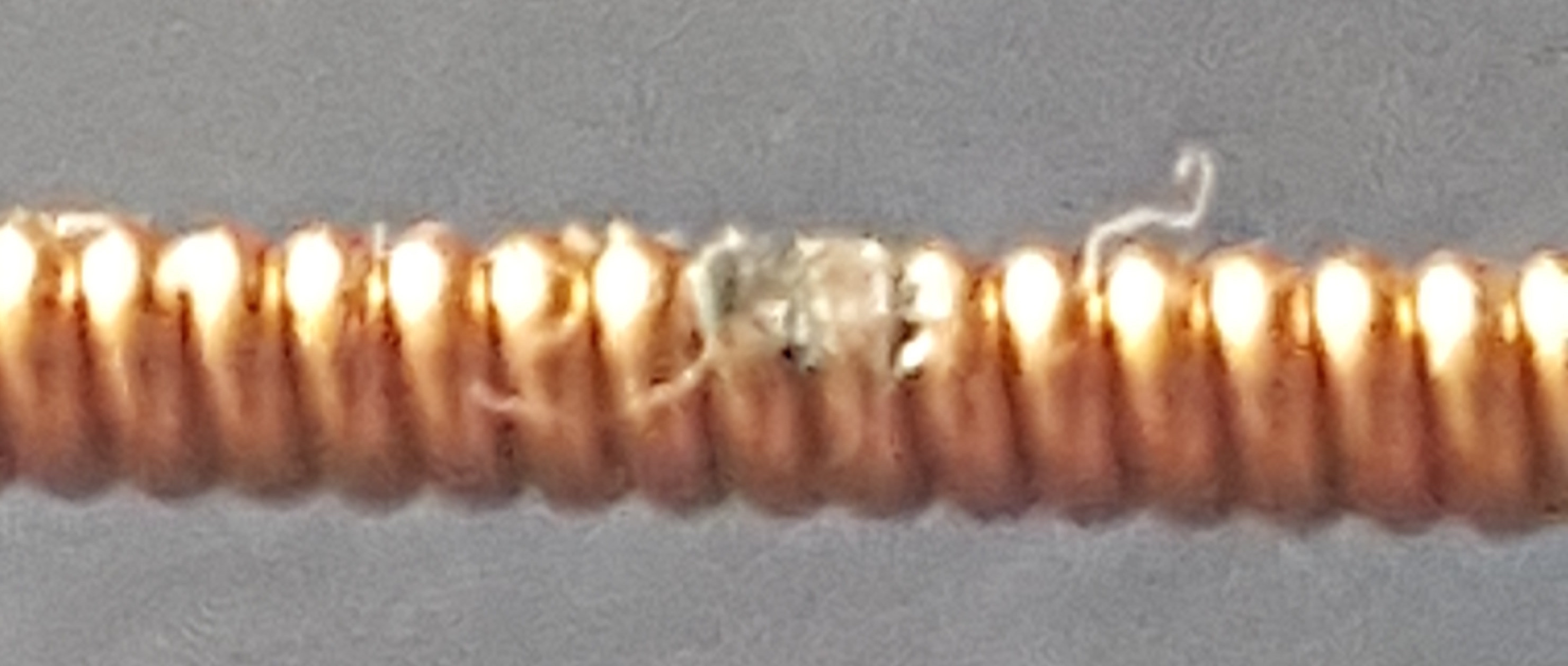
Some string companies coat the wrap wire and sometimes coat the whole outside of the string to address corrosion issues. However, a string with an outside coating may also dampen the true tone of the string as well as eventually fray off from normal playing.
Coated strings will not prevent galvanic corrosion. A coated string can be breached by guitar picks and the frets on the neck. Acting like a file, will breach the coating and expose the wrap wire to corrosive elements. Cover coated strings may also dampen the true tone of the string design.
COATED OR UNCOATED
In most cases, many recording artists may use uncoated strings in recording sessions to maximize the full tone potential of the strings and the guitar but opt for a coated string on stage due to touring and climate changes.
However, with Core-Bond ™️ Technology, which is uncoated on the outside, it will not fray, will retain its tone longer, eliminate galvanic corrosion, and increase the integrity of the string for a very long time.
In some cases, our beta testers claimed that the wound strings lasted up to 1 year with no tone loss. Although it is uncommon for a guitarist to have a string on for a year, this was one beta tester's result.
WHAT IS GALVANIC CORROSION
Galvanic corrosion in a wound string starts immediately after it is manufactured and even more so as it's transported and stored. The difference in the core and the wrap metal alloy causes galvanic corrosion to occur.
CAN A TARNISHED STRING HAVE TONE LOSS

Core-Bond ™️ Technology increases strength, eliminates the chance of core to wrap slippage and makes for a revolutionary new string design, and provides additional time and lifespan. This is how Core-Bond ™️ works...
As a wound string is tuned to key, the core wire stretches and thins slightly, while the wrap wire does not. For this reason, most string manufacturers spin the wrap around the core under core tensions similar to pitch.
As the string vibrates during use, the core wire can also thin slightly, allowing movement of the outside wrap wire to slip, which over time, will cause the coupling to become compromised, and therefore the string effectively starts going dead. Corrosion over time has the same effect.
The Core-Bond ™️ process ensures the integrity of the coupling over a much longer period of time, if not for an unprecedented period of time by "bonding" the relationship of the wrap wire to the core wire.
Stabilization of tuning, the strength of the string, and the loosening at the twist ending by the ball are all obstacles that need to be addressed and eliminated when manufacturing a wound string.
It is virtually impossible for the ball at the end of a Core-Bond ™️ wound string to unravel. The twist lock at the ball on the wound strings becomes "BONDED" together once the final activation process has completed.
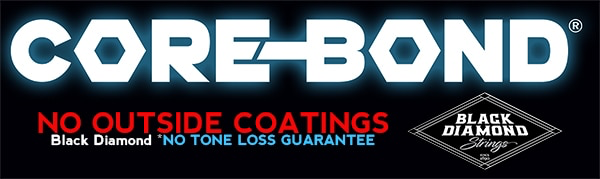
ASSEMBLY BONDING AND THE BLACK DIAMOND #BD6900 WINDING MACHINE
We start with U.S.A. high-grade metal alloy. The assembly of the string begins with the application of core wire placement that is pulled to a specific tension. The outer winding material is then applied by Black Diamond's most advanced string winders in the industry. The BD6900, winders are one-off specialized made machines built by Black Diamond. The BD6900 assists Black Diamond production operators to produce with precision, a Core-Bond ™️ string every 20 seconds resulting in an unparalleled and consistent product. A minimum of 6 computer controllers monitor wrap speed, pull tension, wrap pitch angle, and braking by controlled air pressure, without traditional old-school weights.
This completes the first phase of a Core-Bond ™️ string.
Phase two is the most important process. The Core-Bond ™️ activation phase is to submerge the string in our proprietary treatment bath that activates the inner bondcoat and bonds the core to the wrap wire. The result is longer life, lasting tone, more strength, projection, and output with no outer coating.
WE HAVE CHANGED THE GAME FROM THE INSIDE OUT
COATED VS. NON COATED CORE-BOND ™️ TESTING IN OCEAN WATER
We took a very extreme approach to our testing. By submerging Core-Bond ™️ treated strings in a 5% Saline bath to replicate ocean water, the image below shows results after 96 hours. Keeping in mind, Core-Bond ™️ strings DO NOT have an outer coating to protect the strings. The result is amazing.
Now, we realize a player is not going to put their string in ocean water, but this does validate the protection characteristics of Core-Bond ™️
The strings were clipped at each end to show the acceleration of corrosion at the ends of the exposed steel-plated core wire. Notice seepage of corroded core coming through the center of the coated string on the right, compared to the non-outer coated Core-Bond ™️ treated string left.
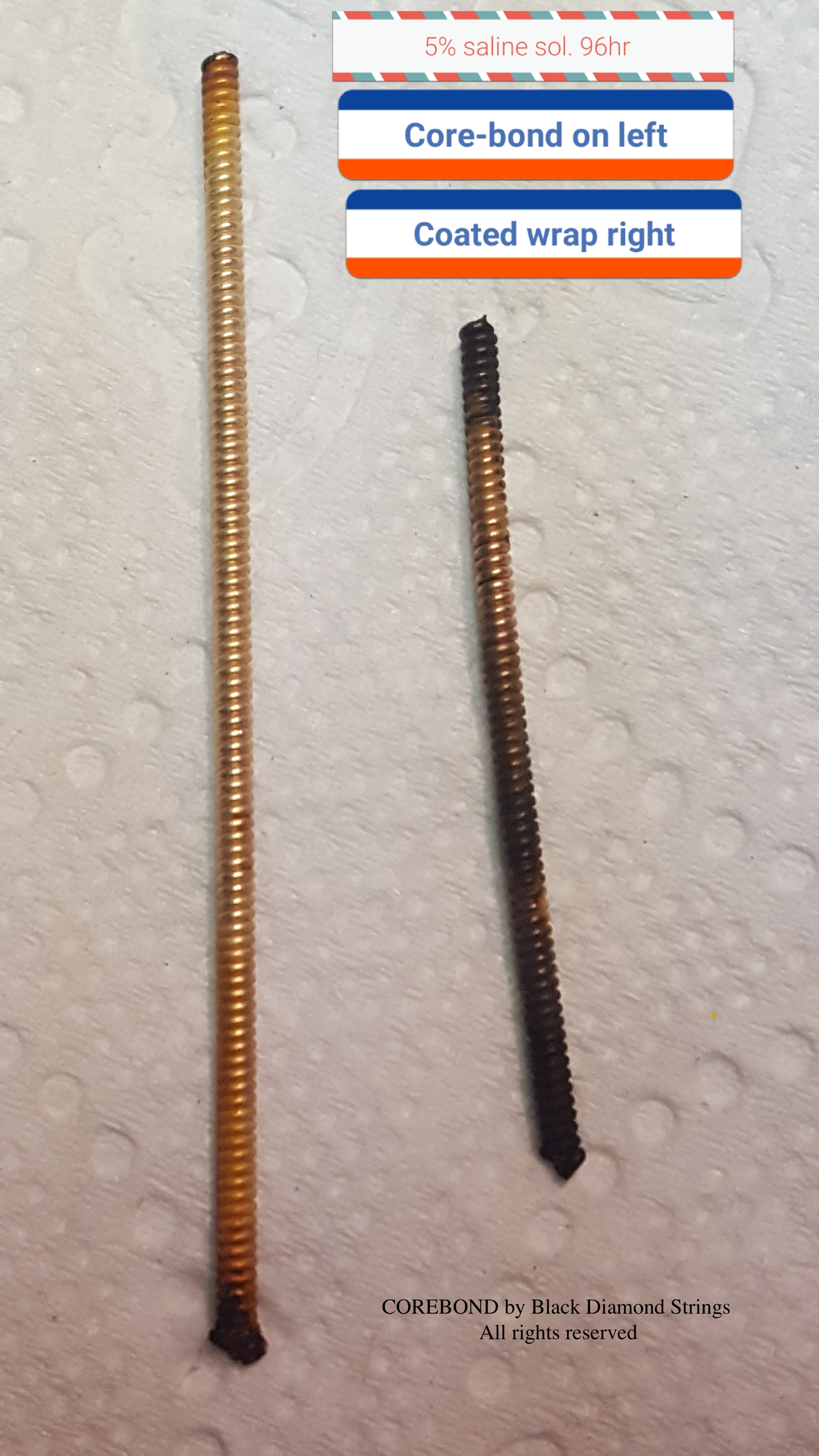
INDUSTRY PLATED COREWIRE vs CORE-BOND ™️
Plated core wire is a widley used and one of the best wires to use when trying to achieve the perfect protection from corrosion. However, wrap wire slippage when tuning /de-tuning along with the degradation of the core through galvanic corrosion caused by the acidic content and dirt in your hands will attribute to sooner than later tone loss.
Steel core wire can rust if it is not plated. Almost every string manufacturer in the industry uses a plated core wire. However, a plated core only helps in the very short term. Anytime dissimilar metals and electrolytes are present without protection, galvanic action will occur. A core that is plated, does not give protection against wrap to core separation due to corrosion which starts from the inside out and subjects the string to premature tone loss and in some cases a dead string.
PATENT - US9424819B1 - Corrosion-resistant wound musical string. Abstract - The method improves the core wire-to-wrap wire bond by using a bond coating between the core and wrap wires that preferably also minimizes the galvanic activity between them. The bondable coating is applied to the core or wrap wires, or both. In one embodiment the method entails creating a coated core wire by annealing bare core wire, bathing the bare core wire in a bondable coating material and removing any excess, drying the bondable coating, making the string using the bondable-coated core wire, and reflowing the bondable coating. In another embodiment the method entails additionally coating the wrap wire with a coating that does not reflow under the same conditions as the bondable coating on the core wire, and winding the coated wrap wire around the bondable-coated core wire before reflowing the bondable coating.
COPYRIGHT 2018 - Core-Bond ™️ by Sfarzo Guitar String Company LLC - IMAGES AND WRITTEN CONTENT USE ON THIS WEBSITE MAY NOT BE REPRODUCED WITHOUT WRITTEN PERMISSION AND CONSENT - CONTACT: INFO@BLACKDIAMONDSTRINGS FOR GRANTED PERMISSION